Oil & Petrochemical – Refineries exhibit unique challenges to boiler plants. Boiler fuel on these sites often have vary considerable in composition especially with respect to sulphur content. High sulphur fuels impose the additional risk of exasperated back end corrosion. Fuel streams can also be heavily contaminated with catalytic particulates that may affect heat transfer of downstream boiler plant.
Design Boiler has many years of experience working with boilers in oil and chemical refineries. Specific examples of expertise applied in this context are presented below:
CO Boiler Circulation Problems: Refinery boilers are required to extract waste heat from refinery gases which contain significant proportions of Carbon Monoxide and other combustible waste refinery gases. They may also be required to operate with supplementary firing, as well as burn the waste refinery gases. .These waste gases can contain catalysis powder that becomes entrained in gas. The catalysis powder can settle onto the boiler heating surfaces especially within the furnace, degrading heat transfer which can retard internal circulation within the boiler, causing tube failures and impair the boiler’s performance. We have investigated the circulation of a number of CO boilers in refineries and can address this problem by fitting sootblowers and by fitting flow measurement equipment in supply tubes.
Boiler Output Limited by Steam Temperatures: The output of a boiler can become limited by high superheater steam and metal temperatures caused by the furnace fouling discussed previously. Catalysis powder settles on the furnace wall and restricts furnace heat absorption significantly raising the gas temperature entering the superheater.. We have investigated and solved persistent furnace tube failure issues on CO boilers in a number of refineries.– Please refer to a related case study here;
Design of Waste Heat Recovery Systems: With the ever-increasing emphasis on waste heat recovery we have been engaged to design waste heat recovery systems for refineries. One such project in the Middle East involved a waste heat recovery system which extracted waste heat from exhaust gas immediately before its entry into the chimney stack. The heat was used directly to preheat naphtha. Read more;.
End of Life Studies: Design Boiler has carried out end of life studies on Carbon Black plants to assess the possibility of either refurbishing boiler plant or relocating it to another site with a more favourable location – i.e. closer to feed stock and lower labour costs. The outcome of this study is still ongoing..
Airheater Corrosion: Design Boiler has investigated causes of airheater corrosion problems and derived effective strategies to mitigate the problem in refinery boilers..
Investigation of Boiler Casing Defects: A low cost package boiler installed in a refinery in Asia experienced constant casing leakage due to poor refractory design and thermal expansion issues. Design Boiler Engineers undertook an extensive finite element assessment of the problem and produced an alternative casing design that effectively addressed the problem.
Design Boiler’s broad range of specialised boiler design services and computer modelling resources are available to troubleshoot and diagnose boiler problems experienced in the refineries and the petrochemical sector.
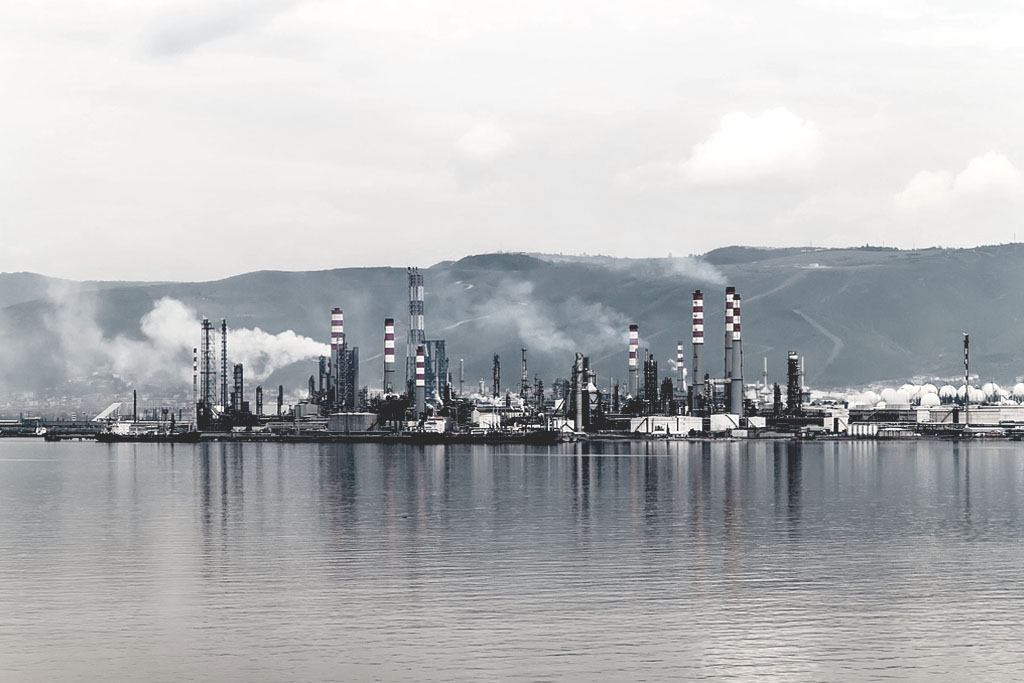